In the ever-evolving digital economy, businesses are compelled to optimize and reduce their operational costs. Inventory management encompasses much more than dead holding of stocks – it is all about technology that enhances purchase scheduling to the market environments. SalesBabu CRM provides plenty of options for businesses to install the automated systems whereby the inventory control is done in the most rational way.
What is Purchase Planning?
Purchasing is an attempt of acquiring products or services for the business or enterprise. In simple terms purchase planning facilitates a structural approach to the management, requesting on purchasing activities, which define the lucrative material purchase plans on what should be purchased, what quantity and where it should be purchased.
The manufacturing companies always need supplies in raw materials – bridging between demand & supply for spare parts and services from the suppliers. Purchase Planning is a necessary process in Inventory management software, where the purchase manager is responsible for all the requisition related to stock in warehouses. The major issues involved during the purchasing procedure is source, price, quantity, quality, time bound and location. If the purchasing task is pursued then inventory is not limited. But if not pursued properly, then the company’s survival is difficult. Planning typically takes place as a component of the budgeting process, where the inventory needed to operate the business properly and to control the cost of the goods with suppliers.
The Importance of Purchase Planning for Manufacturing and Trading Units
In the domain of manufacturing and trading process, the elaborated working operations of inventory software necessitate a well-organized way of purchase planning system. Such implementation of the system includes approaching the suppliers for the periodic acquisition of raw materials. Within such a process, the purchase department must introduce a consistent diligence in acquiring materials that are continuously utilized to shield from the accumulation of dead stock that can adversely affect the business. Sustaining a trustworthy supplier who can continuously provide the requisite materials when needed is beneficial in the organization.
Purchase planning proves to be the keystone for manufacturing and trading units, allowing them to fulfill work that is in progress orders promptly. A well-performed purchase planning strategy not only alleviates the overall expenses connected with purchasing and warehousing but also delivers a vital role in the effective operation and management of a modern warehouse.
Products in consistent consumption that are not prohibitively expensive are the target of inventory control software, enabling for their consistent detection and management.
Major obstacles in purchase planning process
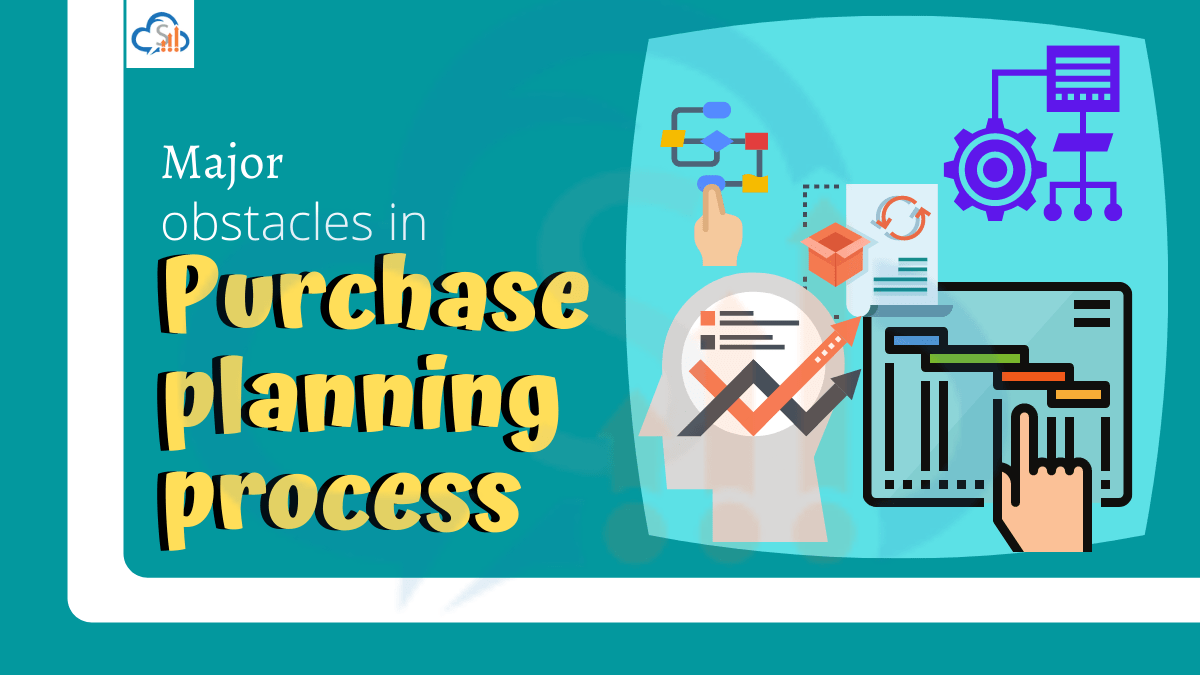
How to do Purchase Planning?
Purchase planning for either manufacturing unit or wholesale or trading unit operation is an important process. Purchasing of the raw materials or goods is to maintain the stock levels. Stock which is required to be maintained in the inventory software, but overstocking or excess of the goods will have a negative impact on the business profits. When purchasing and ordering enough stock, take the benefits of bulk discounts, but balance the inventory and do not over stock.
Read our blog
How to handle & plan Work orders?
Handling the Inventory and tracking of the work order is to keep track of fixed assets, have control on the working capital. Inventory control software will help to get the project costing and the inventory related to the said project.
How to handle Vendors?
Vendor handling is a structured process, wherein the suppliers can be managed by the buyer’s and improve the relationship. Here the deliverables are managed with the vendor, managing compliance, invoices and payments – a work collaboration of the purchase department and vendor.
How to do Product Mapping?
A product mapping is to reduce costing, reduce the storage needs and streamlining the ordering process.
How to do vendor tagging?
Keep the track of inventory, which is important and able to control costs by keeping the inventory software updated. Through the Inventory management system, discovering any kind of discrepancies between inventory results shown related to the vendor tagged products in the software and the physical count.
How to Float Purchase Inquiries?
Purchase inquiry is floated for the requirements necessary in the company. It is raised for a product requirement and interested vendors come up with their proposal to the organisation.
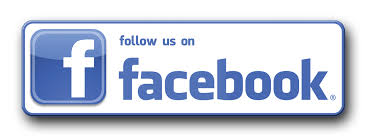
How to handle Vendors Purchase Quotation?
Vendors have provided a quotation to the company for the supply of necessary goods.
How can Compare Vendor Quotation?
When the company receives multiple purchase quotations for the similar products from multiple suppliers, then in inventory management software it is easy to do the comparison and select the best purchase quote.
How to handle Purchase Orders?
Officially the confirmation document is issued by a buyer to the Supplier mentioning the requirement of the products mutually agreed prices.
Is it possible to handle all the Pending Purchase Plans on a single Computer screen?
Yes possible with the help of Inventory Control Software.
How to handle Pending Purchase orders with Vendors?
With the use of this MIS report, companies can see the purchase order status, what quantity is order placed, how many are invoiced and still how many yet to be received from the supplier against the PO issued.
How to increase Inventory Productivity?
In the Online Inventory Management Software, helping to do the reconciliation of the inventory. Through the inventory software, it eliminates the manual way of paper work and maintaining the records, but also streamlines the inventory process.
How to Handle Purchase Bills?
Purchase Invoice processing is handled by the accounts team, through reviewing over Inventory Management Software on the purchases done by the supplier. The process when a company receives goods and purchases a bill against the payment made.
How to handle entire Purchase Returns @ Single Screen?
In order to record the product return, which was purchased from the supplier, it can be done over a single screen. Checking the record and filtering the product when it was purchased.
How to handle material movement cycle?
Handling the material movement is possible with the Inventory software throughout the manufacturing, sales and distribution. During the process it helps in inventory management and product tracking purposes.
How to do Stock adjustment?
In the Inventory Management System, stock records with the actual findings of the physical inventory is stock adjustment. The adjustment of the stock either increasing or decreasing due to the inventory discrepancy in account of theft, loss, breakages or the errors in the physical number.
How to fill the Gap Between Purchase & Inventory Tier?
Gaps are areas where the price of a stock is showing up or down because of no or less business. This kind of gap between the purchase and inventory can be filled by stock optimization with the help of Inventory software.
How to Make Purchase Indent?
This is used internally by the company staff during the purchasing process, a request for the material before placing a purchase order to the supplier.
How to Check and Define Product Re-Order Levels?
In the online inventory management Software, inventory reorder level is shown, wherein the company will place a new order or start a production to maintain the stock. Reorder level is to maintain a safety stock.
In what ways do Businesses benefit from the Efficient Inventory management Systems?
It’s possible to expect phenomenal achievements in operations with a breath provided by modern inventory management systems. For example, SalesBabu CRM was used by a manufacturing company to send purchase orders and manage inventory in a way that was visible in the company’s CRM in real time. What did they manage to achieve? 30 % reduction in oversupply and greater cooperation with suppliers, since reconstructions were always made in a timely manner. These stories also bring forth the role that technology plays in the disconnection that is experienced between purchase planning and inventory control. It makes certain that operations run smoothly.
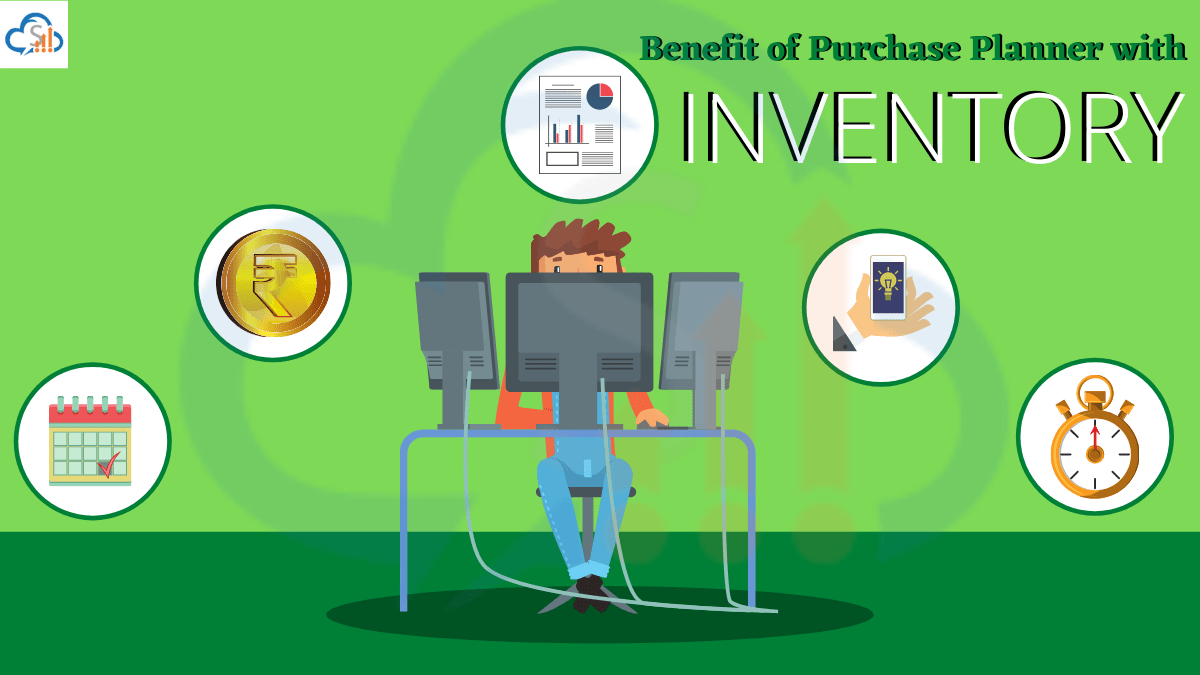
Benefits of SalesBabu Purchase Planner with Inventory On-Demand
- Effective Purchase planning
- Purchase Order Handling
- Enable to Float PI’s(Purchase Inquiries)
- Compare Multiple Quotation with Multiple Vendors
- Get Re-Order Level on Product and Raw Materials
- Handle entire Work Order
- Facilitates Job Work Scheduler Separately
- Enable to make P Q (Purchase Quotations)
- Enable to do multiple GRN against the Partial vendor Order
- Enable for Entire MRN(Material Receipt Note) on one screen
- Manage entire Vendor Bucket
- Get real time Inventory Updates on Stock
- Product Sampling
- Capture Sales Returns
- Vendor’s Mapping with Products
Read our blog
Main factors to be considered while developing a purchase planning
Business needs
Ensuring a solid flow of revenue through good customer relations can be important, but the business needs to be on a firm footing to be in a position to serve the customer. Overstocking will decrease working capital, potentially endangering the ability to grow and diversify. It might also lead to stock obsolescence, reducing profitability. The purchasing strategy, hence, needs to balance business needs against customer needs.
Warehousing and storage capabilities
Warehousing has its own carrying costs that are peripheral to core operations, like staffing and building service costs. It is necessary that the business makes full use of the facilities in order to increase revenue potential. The purchasing strategy should also take the maximum storage capacity into account – overstocking might reduce the available capacity, so orders should fit in with demand. Likewise, the business should be able to move well-stocked items to warehouses where there is a shortage to preserve storage space.
Customer needs
The customer is the primary consideration for any business; without customers, there is no revenue. In the wholesale distribution of goods, the customer is frequently part of a wider supply chain, so reliability is essential. Procurement planning needs to make sure that stock availability at all times, and this should be the main aim when purchasing.
Conclusion
Core Value of SalesBabu Inventory Software India is that it can track entire stock transactions at micro level and can provide real time inventory status on material. It allows companies to do Effective purchase planning against the stock requirements. Hence, SalesBabu inventory management software allows organization to Manage & synchronize entire Purchase Plans, Pending Purchases, Vendor & purchase Quotations and Purchase orders on single computer, which enables inventory manager to keep track of all the Stock Movement (Inward & outwards) and also reduces the operational cost.
To conclude, it is apparent that coming up with an efficient way of dealing with inventoriable goods is pivotal to the success of any business. Such endeavors can be effortlessly achieved by adoption of sophisticated technology such as the SalesBabu CRM tool which considerably reduces manual interventions, enables efficient planning and quick turnaround time in response to the dynamic market. Following the adoption of ICT as a whole in the present times leads to all companies operating a sturdy business model with measurable scalability in the subsequent periods to come.
SalesBabu Online Inventory Management System provides a robust purchase planner tool on a single screen, where companies can easily manage their purchase quotas, and can schedule their purchase plan effectively.
Get your Inventory Management Software Free trial today……